There is often confusion between the terms logistics and supply chain management. While they are both integral parts of any business that deals with physical goods, but they are not the same. There are some key differences between logistics and supply chain management that we will discuss further in this article. However, understanding the role that each one play can help streamline your business operations and ensure that your goods are getting to where they need to go in the most efficient way possible.
What Is Supply Chain Management?
Supply chain management encompasses the entire process of bringing a product to market, from sourcing the raw materials all the way to delivering the finished product to the customer. In other words, it’s the big picture view of everything that needs to happen in order for your product to be successful. This includes managing inventories, manufacturing and assembly, warehousing and distribution, transportation, and even customer service.
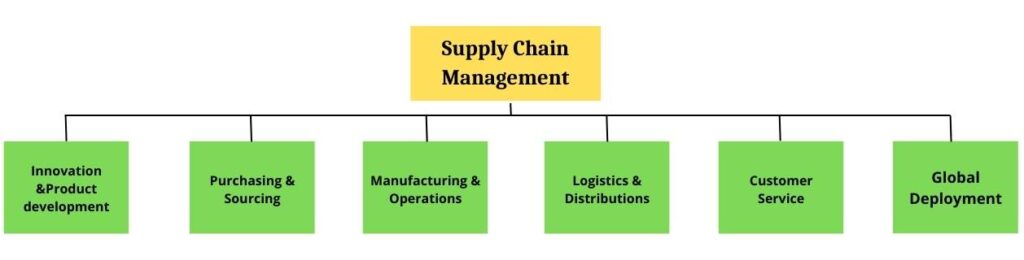
An effective supply chain management system will be able to track the progress of a product at every stage of the process and make sure that each stage is running smoothly. This kind of visibility is essential for businesses that need to move quickly and adapt to changing demands.
5 Types of Supply Chain Management Strategies
There are a few different approaches that businesses can take when it comes to supply chain management. The right strategy for your business will depend on a number of factors, including the size and scope of your operation, the products you sell, and your overall business goals.
1. Make to Stock (MTS)
The make-to-stock strategy is often used by businesses that sell products that are in high demand but have a relatively low degree of customization. With this approach, products are manufactured or assembled ahead of time and kept in stock until they’re needed. This can help to minimize the impact of sudden spikes in demand, but it can also lead to excess inventory if demand falls off.
2. Make to Order (MTO)
The make-to-order strategy is the opposite of MTS, and is typically used for products that are highly customized or made in small batches. With this approach, products are only manufactured after an order has been placed. This can help to avoid wasted materials and excess inventory, but it can also lead to longer lead times and a higher risk of backorders.
3. Build to Stock (BTS)
The build-to-stock strategy is similar to MTS, but with a focus on finished products rather than raw materials or components. With this approach, products are manufactured or assembled ahead of time and kept in stock until they’re needed. This can help to minimize the impact of sudden spikes in demand, but it can also lead to excess inventory if demand falls off.
4. Build to Order (BTO)
The build-to-order strategy is the opposite of BTS and is typically used for products that are highly customized or made in small batches. With this approach, products are only manufactured after an order has been placed. This can help to avoid wasted materials and excess inventory, but it can also lead to longer lead times and a higher risk of backorders.
5. Engineer to Order (ETO)
The engineer-to-order strategy is used for products that are highly customized and made to specific customer specifications. With this approach, the engineering and design process is started after an order has been placed. This can help to ensure that each product is exactly what the customer wants, but it can also lead to longer lead times and a higher risk of backorders.
What Is Logistics?
Logistics is a subset of supply chain management that deals specifically with the transportation and storage of goods. In other words, it’s the nuts and bolts of getting your product from point A to point B. This includes planning and coordinating all of the resources needed to make sure your goods arrive on time and in good condition. An effective logistics operation will be able to track shipments and manage transportation routes to ensure that your product is delivered as efficiently as possible.
Types of logistics management
1. Inbound logistics
Inbound logistics refers to the process of receiving and storing goods that are being shipped to your business. This includes managing incoming shipments, unpacking and inspecting products, and storing them until they’re needed.
2. Outbound logistics
Outbound logistics refers to the process of shipping products from your business to your customers. This includes picking and packing orders, loading shipments, and managing transportation routes.
3. Final mile logistics
Final mile logistics refers to the last leg of the shipping process, from the distribution center to the customer’s doorstep. This includes managing local delivery routes, tracking shipments, and providing customer service.
4. Reverse logistics
Reverse logistics refers to the process of returning products from customers back to your business. This can include managing returns, repairing or refurbishing products, and disposing of damaged or defective goods.
The Difference Between Logistics and Supply Chain Management
While both logistics and supply chain management are essential for businesses that deal with physical goods, it’s important to understand the difference between the two. Here are some key points to keep in mind:
- Supply chain management is the big-picture view of everything that needs to happen to bring a product to market, while logistics is the planning and coordination of the transportation and storage of goods.
- An effective supply chain management system will be able to track the progress of a product at every stage of the process, while an effective logistics operation will be able to track shipments and manage transportation routes.
- Logistics is typically focused on cost optimization, while supply chain management looks at end-to-end optimization of the entire process.
- Logistics is concerned with finding the most efficient way to move goods, while supply chain management is concerned with finding the most efficient way to manage all aspects of the supply chain.
- Supply chain management includes logistics, but logistics does not include supply chain management.
- Logistics focuses on the physical movement of goods, while supply chain management considers a variety of stakeholders such as suppliers, distributors, and customers.
- Logistics looks at the physical flow of products, while supply chain management takes a more holistic view and looks at the financial and information flows that are part of the process.
In conclusion, both logistics and supply chain management are vital for businesses that deal with physical goods. Understanding the difference between the two can help streamline your operations and ensure that your product is delivered in the most efficient way possible.